Story Highlights
- Manufacturing has enjoyed a storied history and recent good workplace news
- Manufacturing employee engagement lags behind the national average
- Some companies are successfully bucking the low-engagement trend
Manufacturing has had a storied history in the U.S. From the innovations of the Industrial Revolution, including the introduction of the steam engine, to the creation of the assembly line and the implementation of lean manufacturing, this sector of American life has been the backbone of U.S. excellence.
And the manufacturing sector has seen some good news lately, too. According to a recent report in The New York Times, "… the latest payroll data underscores the striking rebound at American factories, which lost more than 2 million jobs in the recession, but have clawed their way back and recovered more than 1 million positions since 2010."
Yet neither a storied history nor recent gains in the sector have translated into engaged workplace cultures on the factory floor. Gallup found in its State of the American Workplace report that 25% of manufacturing workers are engaged at work. This is eight percentage points lower than the national average of 33% employee engagement, making it the least engaged occupation across the U.S.
What is happening in manufacturing, particularly, to cause this low engagement and create struggling workplace cultures?
Gallup consultants note that today's employees expect to be managed differently than they were in the modern era of manufacturing that began in the 1920s. Contemporary work environments and new trends have employees asking for flex time and individualization in the role.
Manufacturing companies and factories have not kept pace with the rest of the ever-changing work environment, Gallup consultants note, and this may be an impediment to employee engagement. Those in manufacturing see friends and family not only having flex time, but also observe in them a more empowered workforce where one has greater control over day-to-day decision-making on the job. Manufacturing employees want more of that, but their workplace environment may not allow for that kind of flexibility.
Managers who are bound by procedures, along with unions, may also have an impact on engagement. Unions act as a third-party advocate for employees, which is not necessarily a bad thing, Gallup consultants say -- it just requires following more processes and procedures before important conversations and change can occur.
The challenge, then, is for manufacturing leadership to work around some built-in issues and try to make employees feel great about coming to work every day.
Creating the Right Culture
Stryker is one company that has a highly engaged workforce. Eamonn Nestor, senior director of operations at the global medical technology company, said the culture created there from the top front-line leaders is what propels his company's scores higher than the norm.
"Engagement can be something that's treated like a fad," Nestor said, "or it can be treated as a way to brand our company in a certain way that attracts talent."
Nestor said Stryker's use of Gallup's Q12 employee assessment has helped in pinpointing stress points of the workplace and using survey feedback to make improvements companywide. Nestor also cited the program Gallup conducts on strengths and engagement for managers at Stryker. He said this is an example of a tool that works to boost engagement through lifting up the best managers.
Stryker also conducts town halls, where leaders review their employee engagement results, address issues they are seeing from the data and take questions as well. Additionally, Stryker uses Gallup's pre-hire selection assessments for employees and managers, a feature unique to the manufacturing sector. The employees Stryker selects are more engaged and better able to engage coworkers.
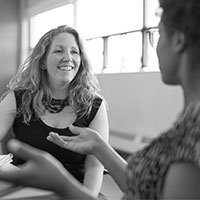
Create Exceptional Workers
Strengthen employee performance with a culture of engagement.
Gallup consultants note there are several companies like Stryker that are implementing these techniques to keep manufacturing employees motivated in a positive way. Consistently, it is managers taking a keen interest who are usually the reason for success.
The best manufacturing managers stay late so they could catch the second shift, for example. They are very intentional about making sure they walk the floor and see all shifts and all people as much as possible, one consultant notes.
What's more, the best managers knew every single employee's name. According to our consultants, some manufacturing leaders with anywhere from 900 to 1,500 employees would know every single person's name. This familiarity helps create relationships and makes people feel like they matter and aren't just a cog in the machine.
What Leaders and Managers Can Do
To create stronger relationships, as a means to boost employee involvement, here are five specific things leaders and managers can do in the factory culture, gleaned from Stryker and other high-performing manufacturers:
- Communicate. Understanding why a company follows a particular process and ensuring that information is properly disseminated are crucial. Another example of good communication is to provide opportunities for customers to visit a particular factory and meet with manufacturing employees. Let the two groups discuss the impact the products have on customers.
-
Allow for more control of work. In manufacturing, much of the work is predetermined, based on the nature of the day-to-day process. Each day and hour might be prescribed, with the employee having little say over his or her schedule. Not surprisingly, this could dampen engagement. Great manufacturing leaders figure out the amount of control they can give back to the employees, which allows them some choice in potentially rote procedures.
-
Create accountability. Great managers work with employees to establish how "we can all be" accountable to the work. When done right, accountability creates higher engagement. It is important to make sure underperforming employees and managers are held accountable, even in situations where management structures may not lend themselves to performance accountability.
-
Make sure people feel like they matter. Perhaps the most important task for a leadership team to figure out -- how to make every associate feel like they matter when they arrive at work every day. This includes making sure every employee understands how they fit into the complex infrastructure of their company. For example, bring customers to the plant to speak with employees about the impact of their products or take "field trips" to customer factories to help plant employees see how the product is used in the different products the client produces. Or hosting breakfasts for the night shift regularly to draw people together in a positive way.
-
Be available, and be engaged. Leaders must be engaged, as employee engagement is a two-way street. Manufacturing managers must be approachable and receptive to employee concerns, and incorporate feedback into enriching future procedures.
In short, to meet organizational needs, leaders have an obligation to coach and develop people. It is not just training, but walking the floor with them, seeing what good practice is, seeing what could be better practice, and giving them feedback on how to move forward. For the present and future, leaders have to get better at coaching and developing others and be intentional in their efforts to do so.